
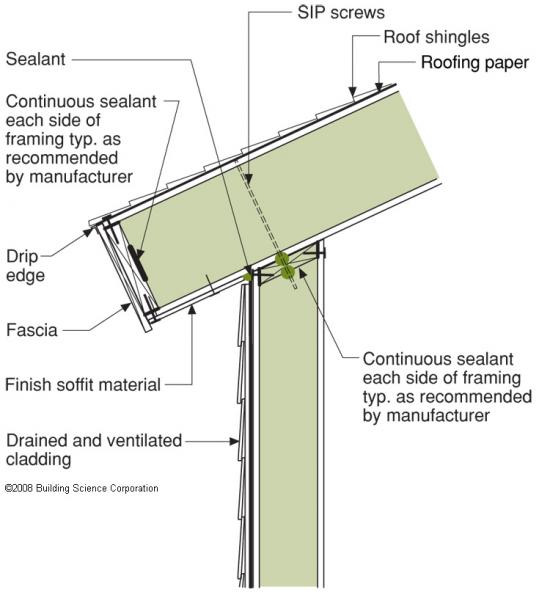
Some manufacturers choose to use polyurethane and isocyanurate as the insulating material. Most manufacturers can also make panels as large as 81´ 281 inches (1.06´ 7.14 m), which require a crane to erect. They are available in almost any size, however, common wall panel are 41´ 81 inches (1.04´ 1.06 meters) and weighs 110 pounds (50 kilograms ). Standard thickness' for either type range from 3.5 to 7.5 inches (89-190 mm) for wall panels and 5.5 to 11.5 inches (140-292 mm) for ceiling panels. It uses a hydrochlorofluorocarbon (HCFC) gas as the expanding agent. Extruded Polystyrene (XPS), with R values of 5 per inch (2.5 cm) of thickness is also sometimes found. Unlike other types of foam insulation, beadboard uses pentane as the expanding agent. This type of SIP has a nominal R-value of about 4 per inch (2.5 cm) of thickness. The majority of SIPs are manufactured with expanded polystyrene (EPS.) This foam is commonly known as beadboard. A company based in Texas has started limited production of a SIP product made with a core of compressed straw laminated to OSB. Some manufacturers are also examining ways of using cementitious or fibrous core insulating materials. SIPs use a rigid-insulation core made of one of three plastics: 1) expanded polystyrene (EPS) 2) polyurethane or 3) polyisocyanurate, a polyurethane derivative. The airtightness of the foam-core house (measured at 0.21 air changes per hour ) and was better than the conventional wood-framed house (measured at 0.27 ach). The FSEC also monitored side-by-side SIP and conventional wood-framed structures for several winter months. The Florida Solar Energy Center (FSEC) found a 12% to 17% energy savings from using SIP construction. Even though SIPs cost more than other construction systems, they require considerably less skilled labor too.
#Aluminum sip panels windows
Additional openings for doors and windows can be cut with standard tools at the construction site.

Many SIP manufacturers also offer "panelized housing kits." The builder needs only to assemble the pre-cut pieces. Testing has shown that a wall panel with two, half-inch (1.3 cm) thick OSB skins is nearly three times stronger than a conventional 2´ 4 inch (5.1´ 10.2 cm) stud wall, even though the SIPs were assembled many times faster than a "stick" framed wall of similar size. Shells can be erected quickly, saving time and money, without compromising quality. The speed of construction when using SIP's is much faster than other types of residential construction, especially if the builder is familiar with them. This makes the building more comfortable, improves energy use in both the winter and summer, and makes the house quieter.

When installed properly, SIP's also provide a more airtight dwelling. The greatest advantage of these panels is that they provide superior and uniform insulation when compared to more common methods of house construction. "stick") framing in almost any construction setting, but are most common in residential construction. SIP construction can replace stud (a.k.a. The most common types of facings are drywall and/or structural wood sheathing such as plywood and oriented strand board (OSB). A SIP consists of carefully engineered laminate with a foam core 4 to 8 inches thick (10.2 to 20.3 cm) with a structural facing on each side. A "foam-core panel," stress-skin panel, sandwich panel, or structural foam panel is the same thing as a Structural Insulated Panel (SIP) which is the modern term for this type of construction.
